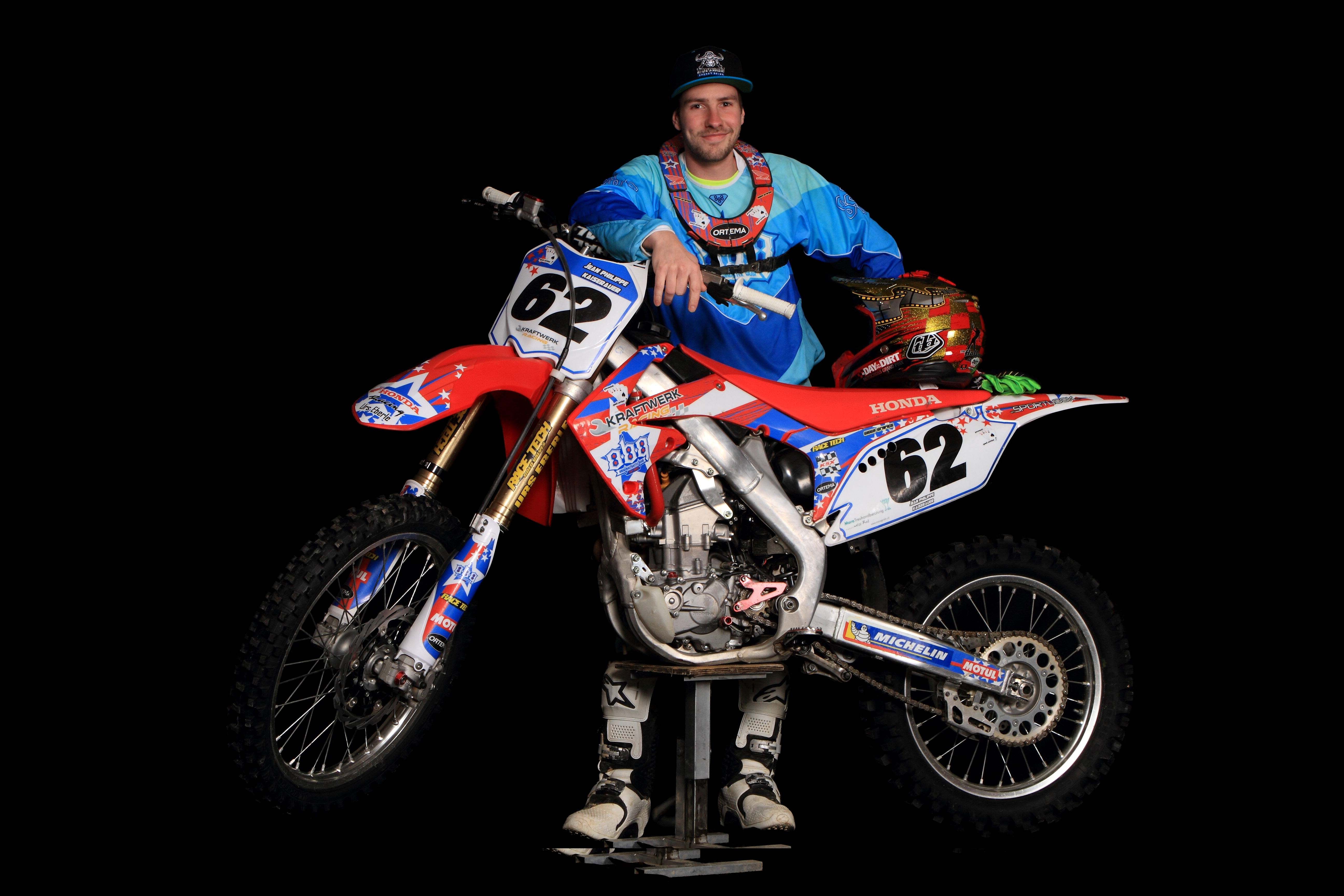
Wir liefern Ihnen individuelle Dekore für alle gängigen japansichen MX-Bikes, sowie für sämtliche KTM-Modelle.
Alle Dekore sind aus einer High Quality Folie, extrem wiederstandsfähig mit einer sehr hohen Klebkraft.
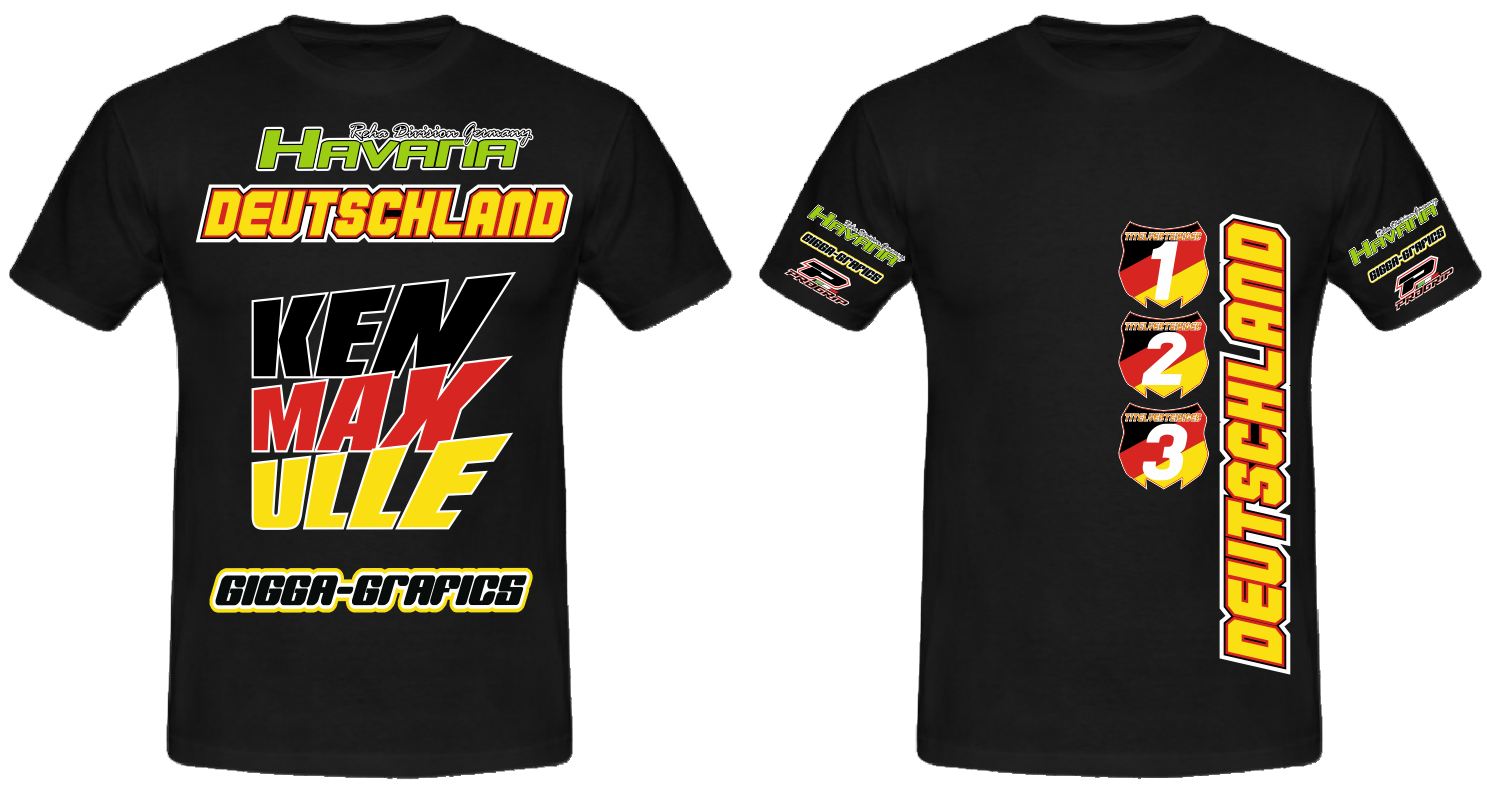
Wir bedrucken Ihre Textilen mit einer speziellen Textilfolie, welche sehr dünn und robust ist. Schicken Sie uns Ihr Kleidungsstück und wir bedrucken es komplett nach Ihren Wünschen.
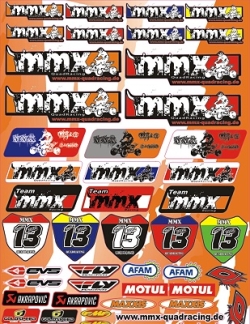
Wir verfügen über eine Auswahl an verschiedenen Stickern. Selbstverständlich fertigen wir auch Sticker nach euren Vorstellungen an. Qualitativ hochwertiger Foliendruck incl. Schutzlaminierung und stark klebend.
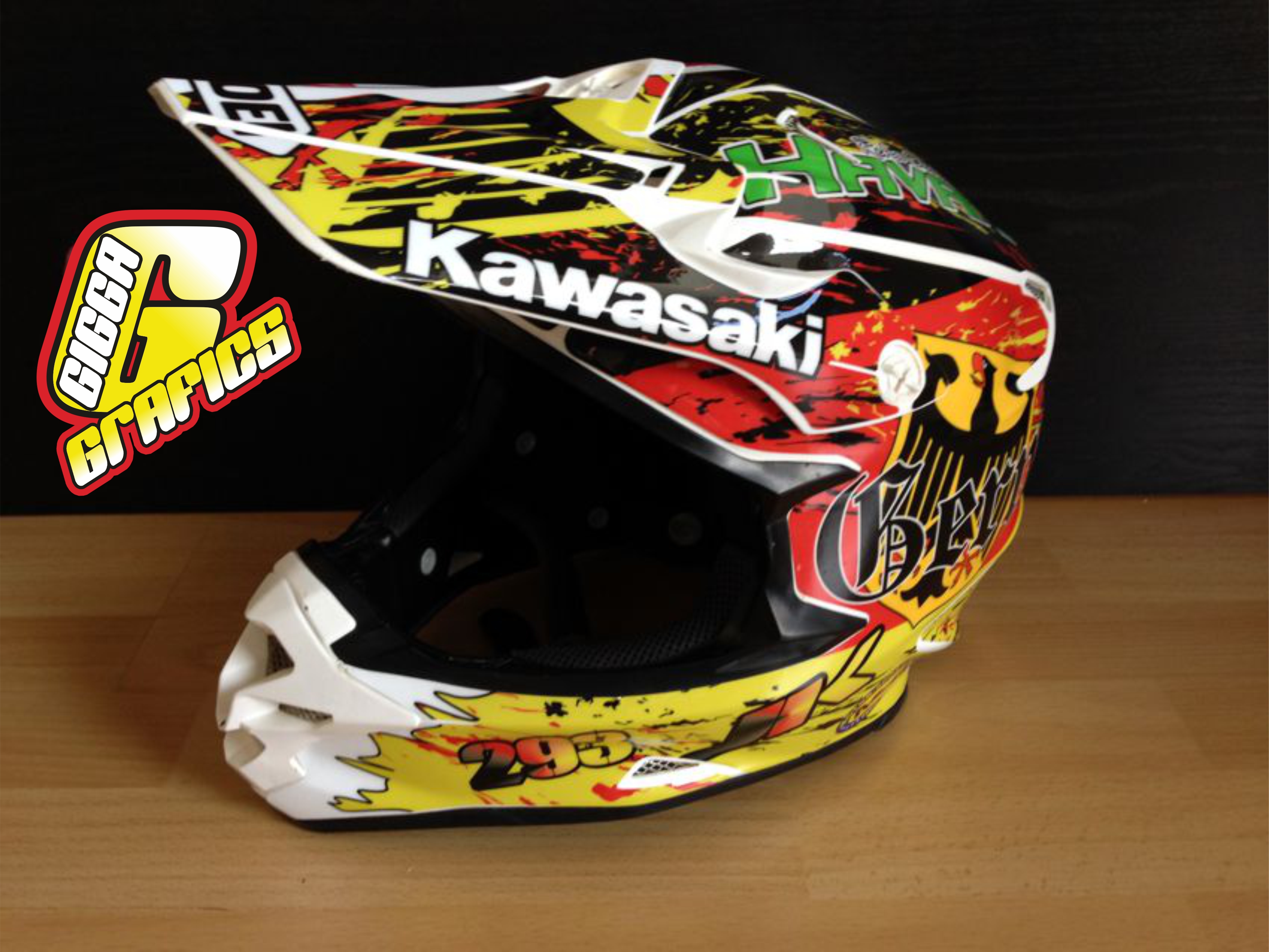
Du möchtest ein individuelles Helmdekor nach deinen eigenen Vorstellungen? Kein Problem! Melde dich mit deinen Vorstellungen & Wünschen bei uns.
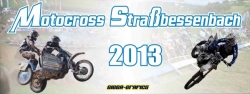
Werbebanner und Werbeschilder nach euren Vorstellungen fertigen wir gerne an.
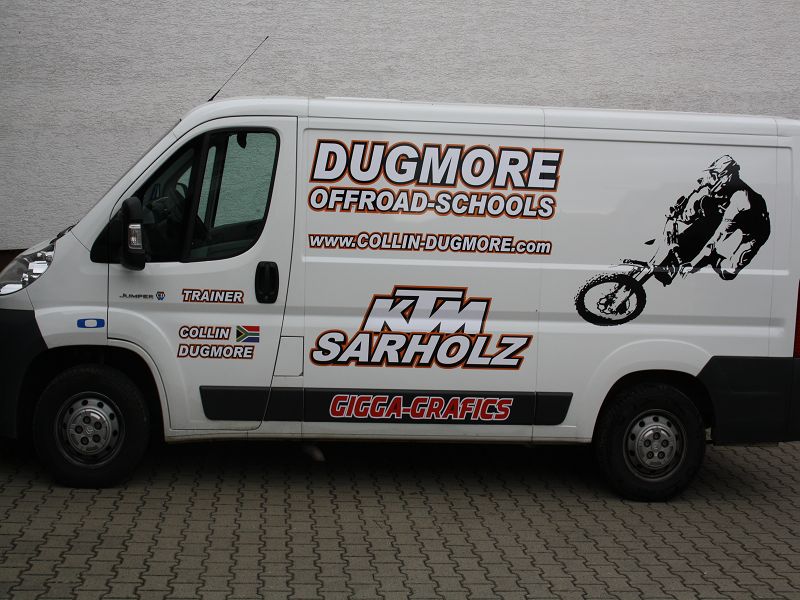
Gestalten Sie ihr Fahrzeug ganz nach Ihrem Geschmack.
Wir bieten hierfür UV-geschützte 3 bis 4 –und 7 bis 10 Jahres Folien an.
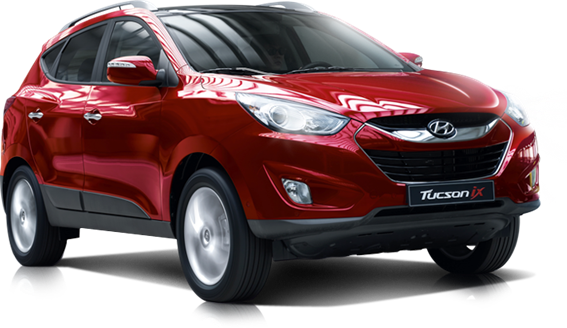
Lorem ipsum dolor sit amet, consectetur adipisicing elit, sed do eiusmod tempor incididunt ut labore et dolore magna aliqua.